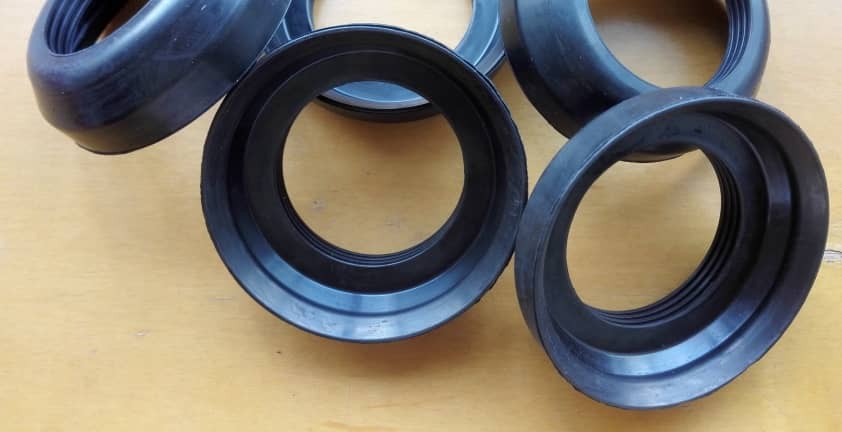
Rubber seals are fundamental components in various engineering and manufacturing processes, offering essential functions that ensure the efficiency, safety, and longevity of machinery and products. From automotive engines to aerospace systems, the role of rubber seals is indispensable. This article explores the significance of rubber seals in engineering and manufacturing, highlighting their types, applications, and the impact they have on the overall performance of engineered systems.
Knowing About Rubber Seals
Rubber seals are designed to prevent leakage, protect components from contaminants, and provide cushioning to reduce vibrations. Made from various types of rubber compounds, including natural rubber, neoprene, nitrile, silicone, and fluorocarbon, these seals are chosen based on their specific properties, such as resistance to chemicals, temperature stability, and flexibility.
Types Of Rubber Seals
- O-Rings: These are circular seals used in a wide range of applications to provide a tight seal between two mating surfaces. Their simplicity and effectiveness make them a popular choice in hydraulic systems, automotive engines, and consumer electronics.
- Gaskets: Gaskets are flat seals used to fill the gap between two surfaces to prevent leakage. They are commonly used in engines, pipelines, and machinery. Gaskets can be customised in various shapes and sizes, depending on the application.
- Lip Seals: Also known as shaft seals or oil seals, these are used to prevent leakage of fluids along rotating shafts. They are critical in applications such as automotive engines, gearboxes, and pumps.
- U-Seals: Shaped like the letter “U,” these seals are used in applications requiring high pressure and high load capacities. They are commonly found in hydraulic and pneumatic systems.
- Custom Seals: For specialised applications, custom rubber seals are designed to meet unique requirements. These may include specific shapes, sizes, and rubber compounds tailored to particular environments or functions.
Applications In Engineering
In industrial machinery, Selectlok rubber seals are essential for ensuring leak-proof operation and extending the lifespan of critical components by effectively preventing contaminants from entering and maintaining the system’s efficiency. Rubber seals play a crucial role in numerous engineering applications, including:
Automotive Industry:
In automotive engineering, rubber seals are essential for ensuring the proper functioning of engines, transmissions, and other critical components. They prevent oil and coolant leaks, protect against dust and moisture ingress, and reduce noise and vibration. For instance, valve cover gaskets and oil seals are vital for maintaining engine integrity and performance.
Aerospace:
In aerospace engineering, rubber seals must withstand extreme temperatures and pressures. They are utilised in environmental control, hydraulic, and fuel systems to guarantee leak-proof operating and uphold the dependability and safety of spacecraft and aero planes.
Industrial Machinery:
Rubber seals are integral to industrial machinery, where they protect components from contaminants and maintain operational efficiency. They are used in pumps, compressors, and conveyors, where they help in reducing wear and tear and extend the life of the equipment.
Marine Applications:
In marine engineering, rubber seals are used to prevent water ingress in various applications, including hull fittings, engine components, and sealing around portholes. They must resist seawater corrosion and withstand harsh environmental conditions.
Manufacturing And Performance Considerations
Several considerations need to be taken into account when choosing rubber seals for a certain application in order to ensure optimal performance:
Material Compatibility:
The rubber compound must be compatible with the fluids or gases it will be exposed to. For instance, silicone rubber is preferred for high-temperature applications, whereas nitrile rubber is frequently used for oil seals because of its superior resistance to petroleum-based fluids.
Temperature And Pressure Ratings:
Rubber seals must withstand the operating temperature and pressure of the application. Some seals are designed to function in extreme temperatures, while others are suited for moderate conditions.
Durability And Wear Resistance:
The durability of rubber seals affects the longevity and reliability of the equipment they protect. High-quality seals are designed to resist abrasion, chemical attack, and environmental degradation.
Design And Customisation:
Custom-designed seals can address specific application needs, such as unique shapes, sizes, or special properties. Manufacturers often collaborate with engineers to develop seals that meet precise requirements, ensuring optimal performance.
Impact On Engineering And Manufacturing
The use of rubber seals in engineering and manufacturing significantly impacts the performance and efficiency of machinery and systems. By preventing leaks, protecting against contaminants, and reducing vibrations, rubber seals contribute to:
- Enhanced Reliability: Seals help maintain the integrity of systems, reducing the risk of failures and ensuring consistent performance over time.
- Increased Safety: Proper sealing prevents hazardous leaks and ensures that critical systems operate safely, which is particularly important in high-risk industries like aerospace and automotive.
- Cost Savings: Effective seals reduce maintenance and repair costs by preventing leaks and damage to components. This leads to lower downtime and extended equipment life.
- Environmental Protection: By preventing leaks of harmful substances, rubber seals help protect the environment and ensure compliance with environmental regulations.
Conclusion
Rubber seals are essential parts of engineering and industrial processes since they guarantee the dependability, security, and effectiveness of different machinery and systems. Their diverse applications and the range of rubber compounds available allow engineers to address specific challenges and requirements, ultimately contributing to the success and longevity of engineered products. Rubber seals’ role will continue to change as technology develops and new materials and designs appear, spurring advancements in engineering and manufacturing procedures.